
Metalite Truss Systems of FL has been offering value engineering as a service to our customers based on our vast experience and “hands-on” Florida based engineers. Learn more about the Steel Deck Institute by visiting their website. Our vast experience has determined our process to be the most effective, flexible and efficient use of both materials and labor, which means reduced material and labor costs for our customers. roof framing to accommodate snow drift loads that were not necessary when the building was originally designed and constructed. fabrication of their open web steel joists, including sloped or curved top chords. Framing members are typically spaced at 16 or 24 inches on center, with spacing variations lower and higher depending upon the loads and coverings. and cold-rolled steel shapes, bars, sheet, and strip. We order stock lengths, minimizing material sorting, saving valuable time. Examples of cold-formed steel that would not be considered framing includes metal roofing, roof and floor deck, composite deck, metal siding, and purlins and girts on metal buildings. Steel Roof Deck Systems Deck Specifications Scissor (Top & Bottom Chord sloped) Truss Common Truss Profiles: Howe (Double Pitch) Truss Semi Howe (Monoslope) Mansard Truss
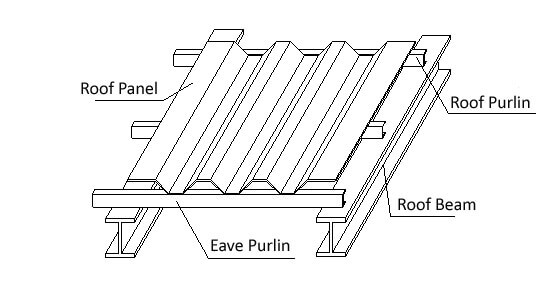
On-site fabrication also cuts time from the process, reduces labor costs and eliminates the need for “piggy-back” truss designs. On-site fabrication by experienced crews helps ensure a quality product by eliminating the risk of damage to the product during loading, shipping and unloading from the shop to the job site. Roof trusses are fabricated onsite in accordance with shop drawings and specifications utilizing jigging systems to ensure consistent component placement and design. From steel-to-steel connections to full-scale lateral solutions and curtain wall connectors, we remain committed to developing new technology that helps to advance the cold-formed steel industry. Our experienced staff prides themselves on performing onsite fabrication and complete installation. With more than 50 years of experience in product design, testing and manufacturing, Simpson Strong-Tie provides comprehensive structural solutions for cold-formed steel construction.

Fewer parties involved means simple coordination, greater efficiency, and less error. By choosing a turn-key truss system from one source, you eliminate a need for others to be involved in the roof truss and/or metal decking component of your project. Our truss package includes designing, engineering, fabrication and complete installation services. offers a fully Florida engineered Cold formed-Light Guage Metal truss system designed for commercial construction projects. The design of the structures were shaped to fall in line with the architect’s vision.Products & Services Cold-Formed Steel Roof Trusses Truss Specifications “In total there were several hundred prefabricated roof panels - because each panel had unique bushings - so there was an enormous variety of technology involved. The spectacular roof-to-basement skylight shaft also had to be considered during design. Several wells were placed on the rooftop for water drainage through the middle of the slopes. Water accumulation into a single corner was prevented by installing vertical gutters on the prefabricated panels while they were still at the factory. Geometric challenges were particularly emphasized by the handling of water loads on the roof’s bidirectionally sloping surface. “Coordinating the steel and wood structures and taking movement joints into account was a big part of our work.” “We did a lot of calculations around how the roof will perform over the coming decades,” says Petri Silvonen. The functionality of the facade connections, in terms of building physics, also had to be resolved. The roof, with its long spans and heavy structures, also had to withstand the architectural detail of the departure hall’s massive, wooden suspended ceiling.

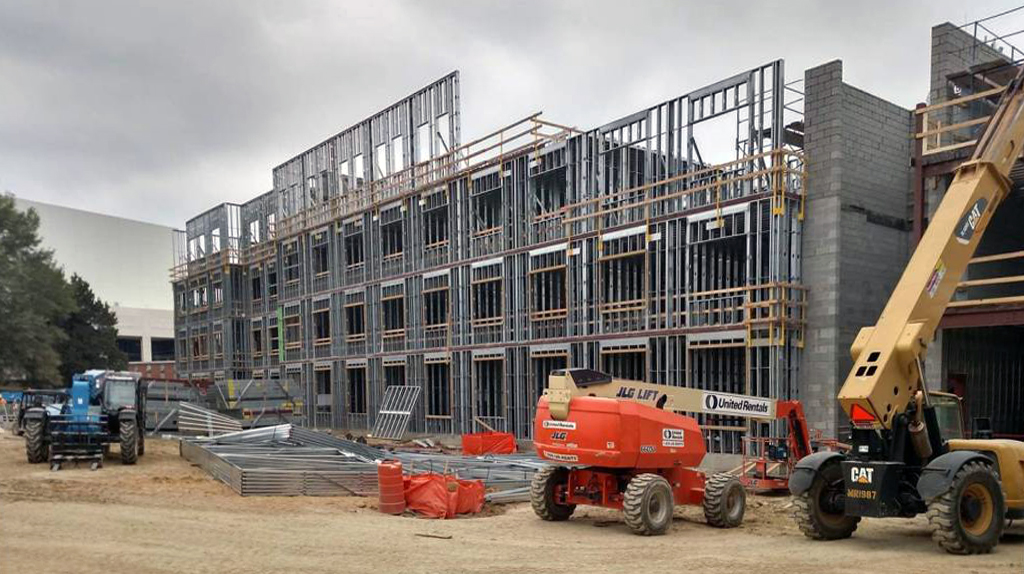
The design stage for the terminal’s sloping roof and prefabricated panels lasted six months.
